New Way Automation vs Traditional Systems: Which Fits Your Business?
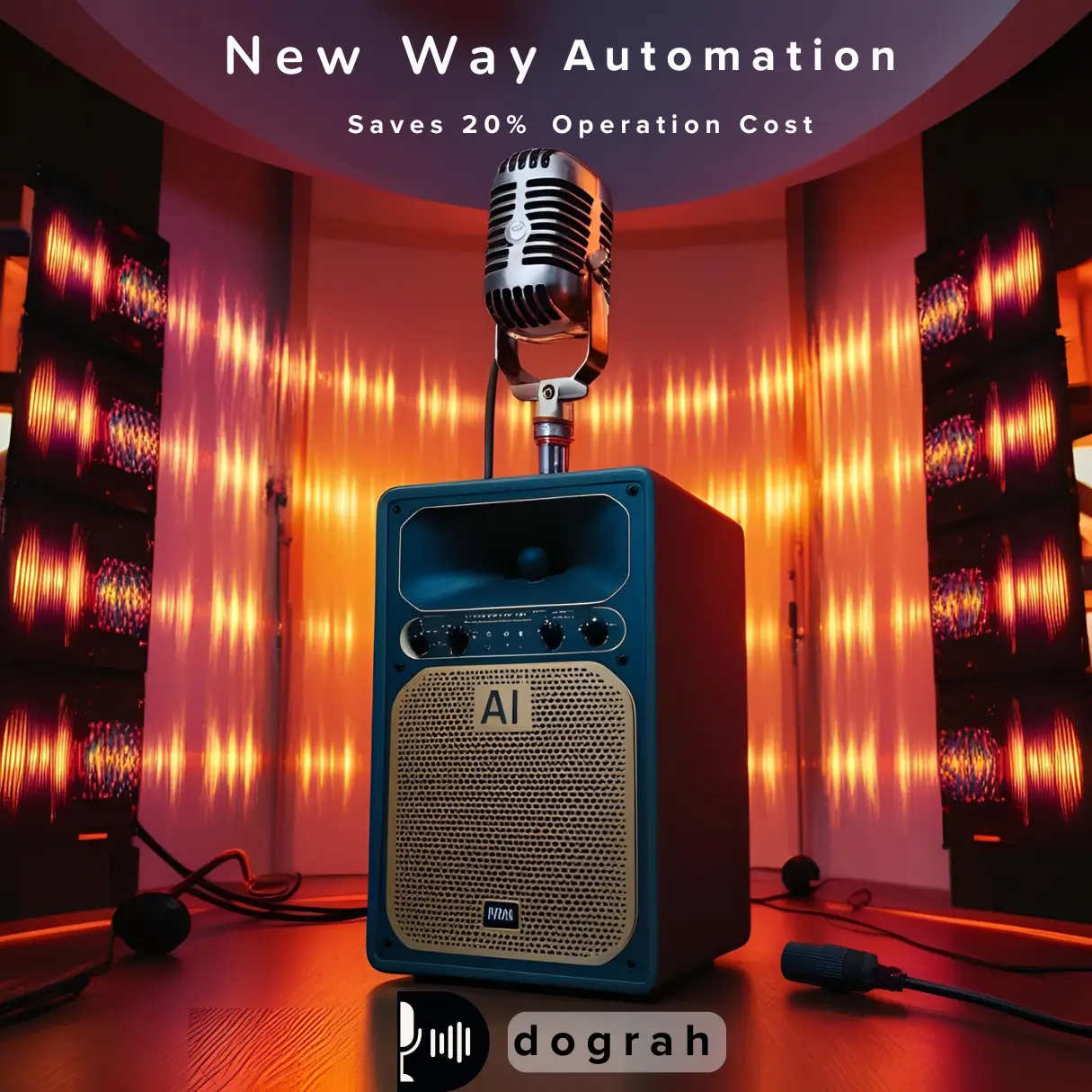
Businesses can and boost their operational capacity by 11% through new automation implementation. The choice between traditional systems and modern automation solutions becomes crucial for businesses of all sizes, from small companies to growing enterprises like NewWay Automation that generate $1M-$5M in revenue save approximately 20% in costs.
McKinsey's research shows that companies excelling at digital transformation automation prioritize strategic differentiation over cost savings alone. The business landscape changes fundamentally when automation reduces waste and enhances accuracy and precision. The transition brings significant challenges to consider. Industrial robots have and 1.6 points for women. Additionally, Korn Ferry projects a skills gap that might result in $8.5 trillion lost revenue by 2030 reduced employment by 3.7 percentage points for men.
Our comparison between traditional systems and NewWay Automation will examine system architecture, implementation requirements, performance metrics, and operational constraints. This analysis will guide you toward the solution that best matches your business's needs.
System Architecture Comparison: Traditional vs NewWay Automation
Modern automation architectures are fundamentally different from traditional systems in their design, adaptability, and how they work with other systems. Let's get into these differences in three key areas.
Mechanical Relay Logic vs PLC-Based Control Systems
PLC-based systems have brought about one of the most important changes in industrial control, replacing relay logic. Traditional relay logic systems were once the foundation of industrial automation. These systems needed physical wiring changes for any modifications to their function. PLC's on the other hand, can be reprogrammed without touching any physical wiring.
Relay logic still works well for small, simple control systems because it's cheap to set up and easy to fix. The cost and wiring complexity of relay solutions quickly become a bigger problem than PLC alternatives as processes get more complex. PLCs also give you more programming options. They can handle complex tasks better and work well with other industrial control systems.
PLCs are a big improvement over relays in terms of reliability. Their sophisticated design and high-quality components make them less likely to fail. They need less maintenance because they have fewer moving parts that can wear out.
Manual Assembly Lines vs Robotic Workcells
Robotic Workcells are giving traditional manual assembly lines a run for their money. Human workers are great at being flexible and making decisions. Robots shine when it comes to strength, endurance, speed, and accuracy. The โhuman labor runs between $16-$30 per hour plus overtime, while robots only cost about $1 per hour to operate cost difference is substantial.
Collaborative assembly systems (CAS) offer the best of both worlds. Humans and robots can safely work together in these systems. This setup combines robot consistency with human skill, which takes automated assembly to new levels of flexibility. When tasks are properly divided between humans and robots, these systems work better than either traditional manual or fully automated assembly systems.
Centralized Control vs Distributed Automation Networks
Control distribution is another key debate in automation architecture. Traditional centralized systems put all control functions in one place. Distributed systems spread components throughout operational areas.
Centralized control makes things simpler to start up. You only need to manage one PLC program, and hardware costs are usually lower. Distributed automation responds faster because decisions happen closer to where problems occur. This cuts down on communication delays.
that you find in centralized designs. Growing businesses love them because they can be implemented and expanded in phases without much downtime Distributed systems don't have the single point of failure.
Both approaches have their strong points depending on what a business needs. The best solution often combines elements from both.
Materials and Methods: Implementation Requirements and Setup
Setting up automation solutions needs complete preparation of physical facilities, hardware components, and system integration frameworks. Businesses must understand these requirements to evaluate their automation options properly.
Infrastructure Needs for Traditional Systems
Traditional automation systems rely heavily on resilient infrastructure throughout the enterprise. These systems need more than simple utilities like electric power and communication networks. They require extensive information infrastructure with high connectivity and compatibility. Database management systems are the foundations that serve as main interfaces for users, storage devices, and communication networks. Manufacturing activities generate massive data volumes. The Boeing 777 represents this scale with 1.5 million parts.
The manufacturing system works only as well as its supporting information technology in traditional implementations. This creates a "weak-link" situation that requires substantial upfront capital for development and integration. The setup typically takes months of feasibility studies and programming to achieve error-free automation.
NewWay Automation Setup: Robotics, CNC, and Vision Systems
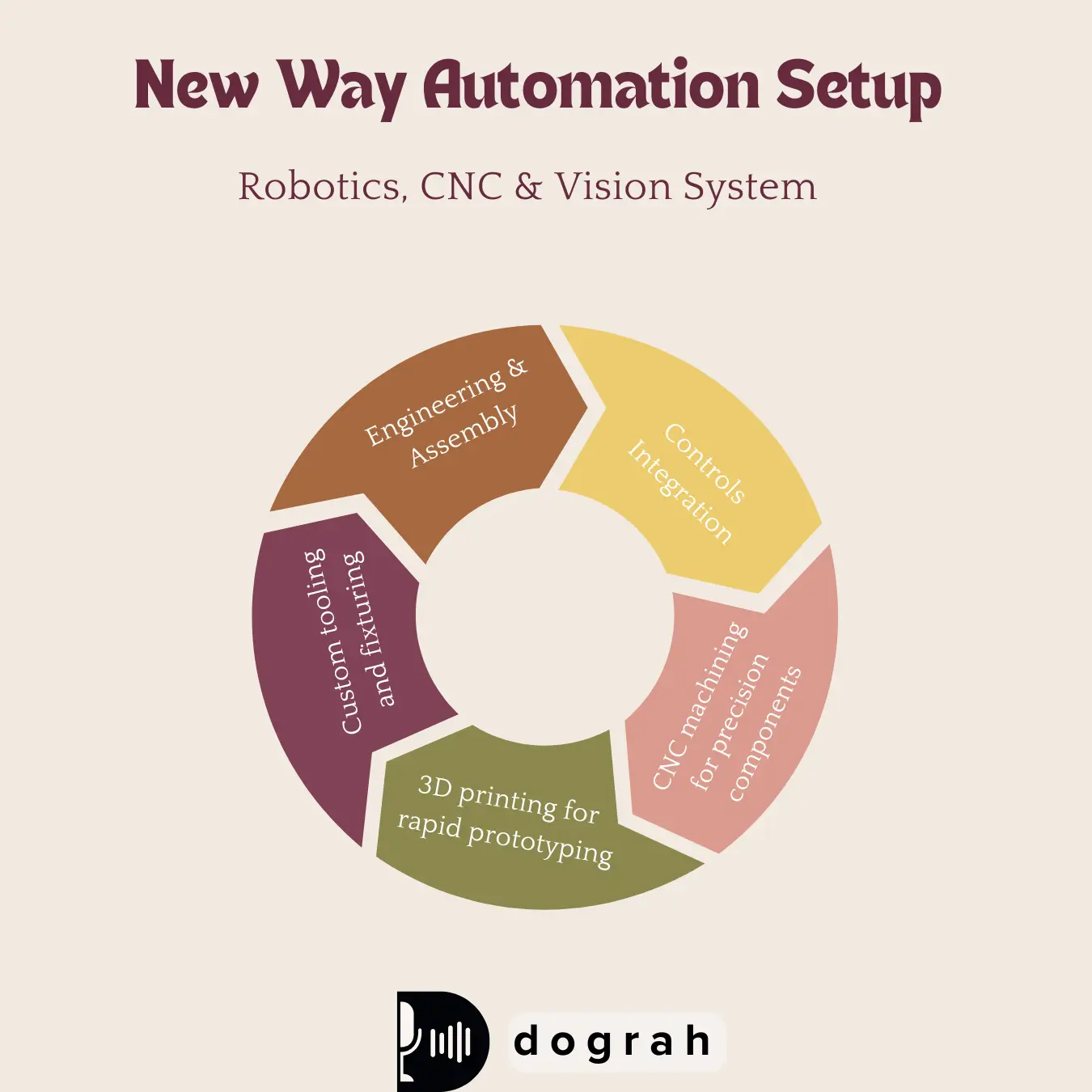
NewWay Automation offers various setup capabilities:
- Engineering and assembly
- Controls integration
- CNC machining for precision components
- 3D printing for rapid prototyping
- Custom tooling and fixturing
Vision systems play a vital role in NewWay setups. They combine digital cameras, image analysis software, and sensors to process visual data. Modern vision systems use both traditional computer vision and AI approaches for specific purposes. AI handles complex image analysis for vehicle detection and license plate identification. Traditional computer vision excels at simple tasks like optical character recognition and achieves 95% accuracy.
Integration with ERP and MES Platforms
Connecting automation with Enterprise Resource Planning (ERP) and Manufacturing Execution Systems (MES) creates powerful synergies. Proper integration helps exchange data between production equipment and management systems instantly, which improves manufacturing process visibility.
Integration optimizes workflows by automating inventory management, production scheduling, and quality control tasks. This reduces lead times and minimizes waste. MES works as a central hub that collects data from automated equipment and sends it to ERP systems. This eliminates manual data entry and paper-based documentation.
The system needs reliable APIs and data synchronization protocols to integrate effectively. Many organizations find success with phased implementation. They deploy pilot projects to test automation solutions before full-scale rollout.
Results and Discussion: Performance, Cost, and Scalability
Businesses are adopting new way automation because of measurable improvements in cycle times, labor costs, and scalability. Decision-makers can learn about traditional versus automated approaches through these metrics.
Cycle Time Reduction with Robotic Automation
Robotic systems cut production cycle times in manufacturing operations. Automated robotic systems can in linear motion tasks and by a factor of 10 in contact-force tasks. Robots maintain consistent speed and precision without getting tired, while human operators naturally slow down during long shifts reduce cycle times by a factor of 4.
Robots in automotive manufacturing work on different vehicle components with extreme precision at the same time. This teamwork leads to faster assembly than manual labor, which means increased production capacity. The system also lets previously sequential tasks run in parallel, which cuts overall processing time substantially.
Labor Cost Comparison: Manual vs Automated Systems
The numbers make a strong case for automation adoption:
- Manual labor costs between $16-$30 per hour plus overtime, whilerobot operation costs about $1 per hour
- Companies in financial services have saved 20% to 60% through automation
- Organizations with 500 employees can lose over $1.47 million yearly from repetitive tasks
A recent case study showed how an automated palletizing system eliminated four vacant positions while moving existing staff to new roles without layoffs. A manufacturing facility saved $86,800 over three years by switching to automation instead of keeping manual operations.
Scalability Metrics: Modular Expansion in NewWay Systems
Modular automation offers unique scalability advantages. Companies can start small and grow step by step as their production needs increase. This approach helps them adapt to changes in demand without spending too much money upfront.
Production can increase by adding new modules to existing systems without major disruptions. Modular automation's expandable capacity helps manufacturers who now keep 30-90 days of on-site storage to handle supply chain disruptions.
Modular expansion helps companies stay ready for the future. They can update or replace individual modules with newer components to keep their systems current with minimal disruption. This flexibility becomes crucial as production technologies evolve and market demands change.
System Limitations and Operational Constraints
Businesses must think over operational challenges carefully when looking at automation solutions. Both traditional and modern systems have their own limitations that affect how businesses run.
Downtime Risks in Traditional Systems
Traditional automation systems face big downtime risks that cost manufacturers between 5% and 20% in lost productivity. A single hour of unexpected downtime can cost more than $100,000. Manufacturers around the world spend about $50 billion each year dealing with these disruptions. Old equipment causes most unscheduled downtime (44%). Human error comes next at 16%, and lack of time accounts for 15%.
Missing documentation makes downtime last longer. System integrators don't deal very well with this problem. They must work backwards to figure out solutions by tracing wires and drawing schematics. This becomes a real headache with complex systems. Old equipment adds hidden costs too, as aging parts break down more often.
Skill Requirements for Robotic System Maintenance
Setting up robotic systems needs special technical know-how. Maintenance teams must know a lot about hydraulics, pneumatics, and electronics. Troubleshooting tops the list as the most important skill for robotics technicians. The next most valuable skills are preventative maintenance and repair work.
Robotics maintenance pros must understand:
- Electronics basics including microprocessors and circuit boards
- Software maintenance to update programs and spot whether problems come from hardware or software
- Manufacturing systems integration and workflow optimization
Automation cuts down shop floor workers but creates new jobs for specialized maintenance roles. Most technicians start with a two-year associate degree. Many begin with basic education and build their skills while on the job.
Flexibility Constraints in Hardwired Logic Systems
Hardwired control systems come with major flexibility limits. These systems use physical wiring to run fixed logic, which makes changes tough and time-consuming. They work fast through direct connections, but their rigid nature becomes a problem when business needs shift.
Programmable systems are a much better match for adaptability. Traditional hardwired automation needs lots of coding and development. This creates stiff systems that don't grow well with changing business needs. Plus, hardwired systems rely heavily on IT teams to make any upgrades.
The choice between traditional systems and new way automation ended up being about finding the right balance between performance benefits and these operational limits.
Conclusion
Your specific business requirements, scale of operations, and long-term strategic goals will determine whether traditional systems or NewWay Automation works best for you. Our comparison shows how modern automation architectures are fundamentally different from conventional approaches in many ways.
Without doubt, NewWay Automation cuts cycle times for certain tasks and saves 20% to 60% in costs when matched with traditional methods. On top of that, its modular expansion capabilities give businesses the flexibility to adapt to market changes without huge upfront investments up to 10 times faster.
All the same, traditional systems make sense for smaller operations with basic requirements and tight budgets. These 20-year-old solutions are easier to maintain and your workforce needs fewer specialized skills to run them.
Take time to get the full picture of your organization's readiness before automating. Look at your current infrastructure, what your workforce can handle, and where you expect to grow. While automation needs money upfront, growing enterprises find the long-term benefits are worth the investment.
Automation is more of a trip than a final stop. Your system must grow as your business does, regardless of whether you pick traditional approaches or accept new ideas from NewWay Automation. That's why you should arrange your choice with current needs while leaving room to expand - it's crucial for lasting operational success.
Related Blog
- Discover the Top AI Communities to Join in 2025 for innovation and collaboration.
- Learn what makes Voice-Enabled AI Workflow Builders Effective in 2025.
- Discover how Making AI Outbound Calls Work: A Technical Guide for Call Centers can streamline automation and boost call efficiency.
- Explore AI Outbound Calling in 2025: What Actually Works Now to learn proven strategies for effective, real-world voice automation.
- See how 24/7 Virtual Receptionist Helps Small Firms Win More Clients by boosting responsiveness and improving customer engagement.
- Learn how How Call Automation Cuts Outbound Calling Costs by 60%: Virtual Assistant Guide can transform your call centerโs efficiency and savings.
FAQ's
1. What are the main differences between traditional systems and NewWay Automation?
Traditional systems often use hardwired connections and centralized control, while NewWay Automation employs PLC-based systems, robotic workcells, and distributed automation networks. NewWay Automation offers greater flexibility, easier reprogramming, and improved integration capabilities.
2. How does NewWay Automation impact production cycle times?
NewWay Automation can significantly reduce production cycle times. Robotic systems can decrease cycle times by a factor of 4 in linear motion tasks and by a factor of 10 in contact-force tasks. This acceleration is due to robots maintaining consistent speed and precision without fatigue.
3. What are the cost implications of implementing NewWay Automation?
Implementing NewWay Automation can lead to substantial cost savings. While manual labor typically costs between $16-$30 per hour plus overtime, robot operation costs approximately $1 per hour. Companies have achieved cost savings between 20% to 60% in various industries by adopting automation.
4. How scalable is NewWay Automation compared to traditional systems?
NewWay Automation offers superior scalability through modular expansion. Unlike traditional systems, modular designs allow businesses to start small and incrementally scale as production needs grow. This approach enables companies to adapt to changes in demand without large upfront investments.
5. What are the skill requirements for maintaining NewWay Automation systems?
Maintaining NewWay Automation systems requires specialized technical expertise. Maintenance teams need extensive knowledge in hydraulics, pneumatics, electronics, and troubleshooting. They should also understand software maintenance, manufacturing systems integration, and workflow optimization. Most technicians require at least a two-year associate degree.
Was this article helpful?